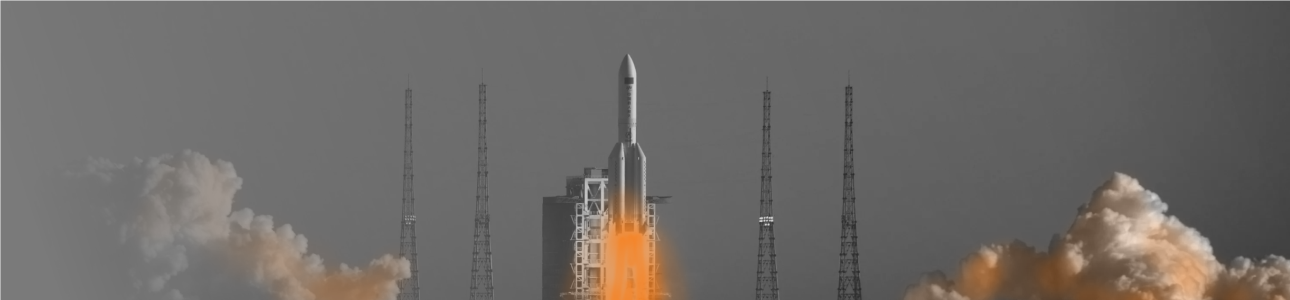
|
Компоненты аэрокосмической промышленности с помощью 3D-принтера по технологии LPBF.
Аэрокосмическая промышленность всегда опиралась на новые, передовые технологии. Сегодня именно 3D-печать открывает новые возможности для разработки и производства даже самых необходимых компонентов. На этом фоне технологии 3D-печати активнее внедряются в космическую отрасль, зная, что технология может удовлетворить строгие требования аэрокосмической промышленности при экономичных общих затратах.
Фокус на скорости и эффективности: экономически эффективное производство прототипов и малых серий играет решающую роль, особенно на быстро растущем рынке аэрокосмической промышленности. Зачастую индивидуальные требования к аэрокосмическим деталям идеально подходят для аддитивного производства. Это также позволяет использовать нестандартные материалы, такие как медные сплавы, которые было бы очень сложно и дорого обрабатывать обычным способом. В аэрокосмической отрасли большинство компаний ищут металлические производственные процессы для изготовления сложных или трудно изготовляемых деталей.
- Компания AM.TECH является ведущим поставщиком систем и материалов для прямого лазерного плавления металлов LPBF (SLM) - процесса производства деталей высочайшего качества на основе порошкового слоя - надежного, воспроизводимого и экономичного.
- Требовательные условия эксплуатации требуют превосходных материалов. AM.TECH предлагает широкий выбор металлических материалов, обеспечивающих оптимальные свойства изделий, включая медь и титан.
- Свобода проектирования - один из основных принципов аддитивного производства, поскольку оно позволяет создавать конструкции и применять компоненты, которые невозможно изготовить традиционными методами. Промышленность может полагаться на решения AM.TECH - у нас самая большая база промышленных 3D-принтеров.
Для вывода микроспутников на орбиту необходимы небольшие ракеты-носители, и спрос на них на рынке постоянно растет. В последние годы отрасль "нового космоса" стремительно развивается. В гонке побеждает та компания, которой удастся вывести в космос наибольшую полезную нагрузку с наиболее эффективной двигательной установкой. Аддитивное производство - ключевой подход к снижению стоимости при сохранении оптимальной конструкции двигателя. Но это работает только в том случае, если привод может быть напечатан в 3D как единая деталь.
3D-печать ракетного двигателя
Позволяет реализовать решающие преимущества при создании ракетных двигателей. Кроме того, можно полностью переосмыслить и создать функциональность компонентов: например, интегрировать внутренние каналы охлаждения в камеру сгорания или объединить отдельные компоненты в единую конструкцию. Результат - новые, инновационные конструкции ракет и самый большой в мире ракетный двигатель, когда-либо изготовленный аддитивным способом в виде одной детали.
![]() |
Самый большой в мире цельный 3D-печатный ракетный двигательВ основе лежит типичная конструкция ракеты, но дополненная внутренними ребрами для оптимального охлаждения. Самый большой в мире цельный 3D-печатный ракетный двигатель. Одной из проблем является размер монтажного пространства и сложные свойства материала. Камера сгорания, напечатанная 3D-печатью из медного сплава, является самой большой камерой сгорания жидкостного ракетного двигателя, напечатанной 3D-печатью в виде одной детали в мире. Высота камеры сгорания составляет 86 см, а диаметр выходного сопла 41 см. На анимации показана полная камера сгорания с компонентами аддитивного и конверсионного производства. Традиционно производство такого типа деталей требует миллионных инвестиций в специализированное оборудование. С помощью 3D-печати вы можете напечатать камеру сгорания, сопло и горловину как единую деталь. Благодаря этому достижению еще никогда не было так просто. |
Крепление антенны для спутника Sentinel
Оптимизация крепления антенны по топологии: компоненты, изготовленные методом аддитивного производства, все чаще используются на спутниках, отправляемых в космос. Это связано с тем, что данная технология отвечает всем важнейшим требованиям: компоненты требуются в небольших количествах, и в то же время основное внимание уделяется весу и снижению затрат за счет экономии материалов.
Например, топологически оптимизированное и аддитивно изготовленное крепление антенны для спутника Sentinel, выполненное из алюминия AlSi10Mg по технологии LPBF (SLM) печати, отличается малым весом и исключительной стабильностью.